Getting Started with LED Flexo Inks: Frequently Asked Questions
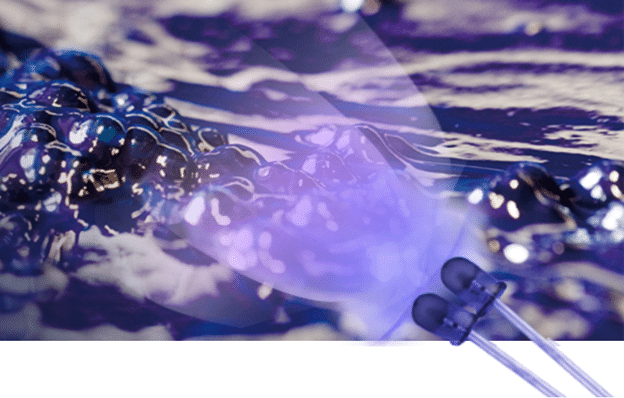
As LED curing systems gain wider acceptance in the Flexographic industry, the benefits of the systems create many compelling reasons to switch. Extended lamp life beyond 30,000 hours, instant on, “cool curing” with minimal heating and distortion of the substrate, reduced energy consumption, consistent depth of cure, no toxic mercury from the lamps and no ozone generation (and therefore no necessity for ventilation), are just a few significant benefits with LED flexo curing technology.
As more and more flexographic LED systems are installed, Zeller+Gmelin has formulated high quality LED flexo inks to help converters take advantage of the many benefits of this exciting new technology. Before “flipping the switch” on either ordering a new press configured with an LED curing system, or retrofitting an existing press with an LED system, it’s important to ask the right questions to ensure you’re purchasing the best system for your future.
Here are some common questions we receive from customers getting started with LED Flexo inks and answers from Zeller + Gmelin Ink Specialists to assist you in your journey into LED technology.
Frequently Asked Questions
Will an LED system really save money?
The short answer is yes. Though each manufacturer has unique cost saving benefits innovated into their LED curing systems, all LED systems are known for achieving big savings in energy consumption. LED curing systems are incredibly more energy efficient and can help converters save money on energy bills and other soft benefits throughout the plant. Also the cost savings attributed to less maintenance, consistent curing, and instant on-off technology keeps your equipment up and running, reducing downtime and increasing profitability.
What is the curing quality of LED compared to UV?
From our perspective, one of the biggest benefits of LED is the consistency of cure, compared to a conventional mercury UV system. With conventional UV curing systems, curing consistency can decline over the life of the bulbs and regular maintenance is required: including cleaning the reflectors, bulb replacement after around 1000 hours (considering the bulb output will continuously decline over the life of the bulb), and maintenance of the other mechanical components of the system.
Alternatively, an LED system offers steady, consistent curing power output for the life of the system, without the steady decline in curing power. With LED curing technology, your ink curing stays consistent – especially important if you’re running low migration work!
Can I run LED Flexo inks on my conventional UV presses too?
Maybe you’re still using UV curing systems throughout your operations and you’re hesitant to make the switch to LED only to end up with two inventories of inks: LED-curable and UV-curable. At Zeller + Gmelin, we adapt our inks to the needs of the market and formulated the 17 Series LED Flexo Inks for “dual cure”, meaning they will cure under both LED and conventional mercury curing systems.
If you’re running operations with both LED and UV curing systems, you only need one inventory of Zeller + Gmelin LED Flexo inks to use throughout your operations. Just be aware that the reverse is not true – UV flexo inks designed for mercury systems will not cure under an LED system.
What are the benefits of LED curing systems, not available on UV systems?
Though LED and UV curing technologies ultimately both cure ink effectively, LED systems have multiple benefits unique to its low heat and energy-efficient characteristics. To begin, UV curing systems have short-wavelength lamps that convert oxygen into ozone, which can irritate your operators and will need to be ventilated – while LED systems create no ozone to vent. LED is also known for its much cooler operations – while LED systems will create some heat in the web, it’s nothing like the heat generated by a conventional mercury system, since those bulbs also emit infrared wavelengths. This also translates into quieter operations.
Additionally, LED systems are instant on and off, with no warm up or cool down time necessary. These benefits make LED systems an excellent option for curing many colors, especially heavy opaque whites, at higher run speeds.
What are the limitations of LED systems?
LED curing has limitations for surface printed clears, like coatings and varnishes. LED is great for “buried” clears, like lamination and cold foil adhesives, but clear surface coatings don’t develop a good level of surface cure with LED. Many of our customers install LED on all but the last unit, where they keep a mercury bulb to cure coatings.
Why are LED inks more expensive than UV inks?
LED Flexo inks, at least right now, cost a little more than comparable conventional UV flexo inks. This is primarily due to the relative “newness” of LED inks in general, which limits available raw materials for formulation. Just like cell phones, computers, and any other new technology, the costs start out higher until that technology becomes more widespread. We expect the cost of LED inks to continue to come down as the technology is adopted into the industry on a wider basis.
Making the Switch to LED Flexo
LED curing systems for narrow web printing are still evolving. Like any other new technology, your decision needs to balance your current need with where the technology has advanced to today and where it is expected to be in the next 6 months. Now that you better understand the benefits and limitations of an LED curing system, you may be ready to take the next step.
At Zeller + Gmelin we are here to assist you through every important ink-related decision. We can put you in touch with our LED curing system partners, and even introduce you to customers who have embraced LED curing, so you can speak firsthand with them to inform your decision.
Talk to your Zeller + Gmelin Account Manager today to discuss your operations and see if it makes sense to step into the world of LED curing systems and inks.