The Basics of Flexo Ink Chemistries, Manufacturing & On-Press Maintenance
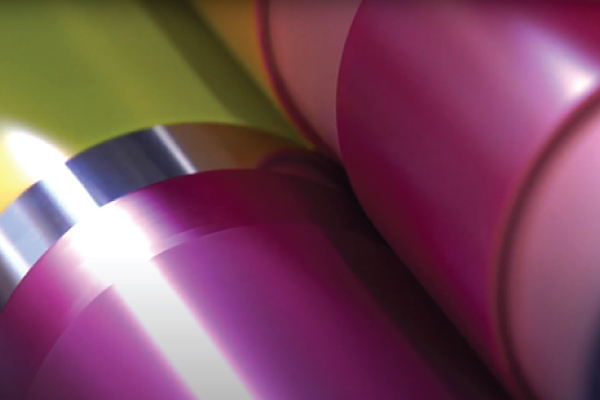

Author: Ed Dedman, Zeller+Gmelin Flexo Product Manager
This article was first posted by the Flexographic Technical Association
Ink—that magical, mystical fluid—delights designers, annoys accountants, inspires inkies and P-O’s press operators! We use it in flexo presses every day, all day, across the country and around the world, yet so many people don’t understand how ink really works, what it can and can’t do, and how to use it best to maximize productivity in the pressroom.
FTA asked me to do an FTA Member Webinar on the basics of flexographic inks. We had good attendance, a lot of questions and a lot of follow-up communications. In this article, I’ll try to recap the information that was conveyed in the webinar, along with a little bit of further detail about some of the topics that were of most interest to folks. I’ll cover the basics of all three common flexographic ink chemistries—water based, solvent based and energy curable. We’ll explore the basic ingredients used in each chemistry, how they work in each type of ink and how they perform their functions on press. You’ll learn how ink manufacturers make these inks in both large bulk form and in small batches. Also covered will be typical quality control (QC) checks used, and the tools and equipment required to perform those checks, both in the QC lab and in your pressroom. Finally, we’ll cover some on-press variables that can affect ink performance and some basic suggestions for troubleshooting common ink problems.
Before we dig too deep, let me just offer three “qualifiers”:
As previously mentioned, flexographic inks are divided into three main categories. Water-based inks are used on wide web flexo presses for applications like paper packaging, overwraps, bags, etc., and in narrow web flexo for products like pressure-sensitive labels, tags, envelopes and the like. Solvent-based inks are used primarily in wide web applications like film packaging, overwraps, bags, pouches, etc.; they see very little use in narrow web, but are occasionally the ink of choice for adhesives, coatings, etc. And lastly, the category of energy-curable inks covers three main energy curing methods—ultraviolet (UV), light-emitting diode (LED) and electron beam (EB). Both UV and LED are in widespread use in the narrow web portion of the flexo industry, with EB used to a much lower degree in both wide and narrow web.
Basic Ingredients & How They Work

The main components in any water-based ink system are the following:

For solvent-based systems, the components are similar, but slightly different:

For energy-curable inks, the components are once again similar, with some significant differences:
In summary, the basic ingredients of each ink chemistry vary mainly in the type of resin system used, and the method of drying or curing used. Each chemistry has its strengths and weaknesses, because each is utilized for different print applications, based on the suitability for the end product. Some colorants work better in one chemistry versus another, due to their relative ability to “wet out” those pigments.
Both water-based and solvent-based inks dry by evaporation, absorption or a combination of both. Energy-curable systems dry by being “cured” after exposure to energy; in the case of UV and LED inks, that energy is light, where for EB inks the energy is a stream of electrons.
Manufacturing Larger Batches
Most ink manufacturers make large batches of common ink formulas, in order to maximize efficiency and manage costs. Most colorants must be “ground” to wet out their surface area in order to be effectively “carried” by the resin vehicle system through the printing process. Some sort of manufacturing method/device must be used that imparts physical energy to the colorant mixture, in order to break it up into smaller particles. Ink companies use machines like bead mills, shot mills, three roll mills and the like for this purpose.
The inks are then typically strained or filtered afterward to capture any large particles. The formula is often completed by the addition of other ingredients needed to make a “finished” ink that is ready for press.
For smaller batch sizes or for mixtures of different colored inks, blending is typically used at an ink company branch facility or a customer inkroom. Blending takes much less physical energy, and can be accomplished by using small mixers, stirrers or through hand mixing with a drill/blade combination, or even a stir stick.


Most ink manufacturers use stringent quality control methods and equipment to make sure their inks are on spec for their various attributes—such as measuring viscosity, seen here—as part of the internal manufacturing process.
Quality Control at the Manufacturer & Print Facility
Most ink manufacturers use stringent quality control methods and equipment to make sure their inks are on spec for their various attributes—color, strength, viscosity, adhesion, gloss—as part of the internal manufacturing process. Tools like a viscometer, grind gauge, proofer, spectrophotometer, gloss meter, pH meter, rub tester and COF tester are used during the development process, as well as during manufacture. Other tools are available for the ink manufacturer as needed, depending on the properties desired in the finished product.
Some of these same QC tools can often be used at the print facility, but some favored by ink manufacturers are cost prohibitive for a printer’s pressroom or inkroom. Typically, the printer can effectively monitor ink condition and suitability for use with tools like a Zahn cup for viscosity measurement for water-based and solvent-based inks (but not for energy-curable inks—these inks are too viscous for using a cup method), a pH meter for water-based inks, a hand proofer, a spectrodensitometer, and possibly a gloss meter, rub tester and COF tester for QC of the finished printed material.
On-Press Variables Affecting Ink Performance
It would take a completely separate webinar and accompanying article to adequately cover the on-press variables that can affect ink performance. Here are a few of the things a printer should be aware of that can affect how an ink performs on press and as a printed product:
Basic Ink Troubleshooting
A few basic tips: In general, when you are troubleshooting, make one change at a time. Always follow your ink supplier’s recommendations. For specific problems, contact your supplier! And always check the basics first—don’t make major changes without confirming you have the right ink for the right job, using the right conditions.
Specific to ink adjustments—in general terms:
For color adjustments:
No matter which type of ink chemistry you use, the bottom line is this: Take care of your ink, and it will take care of you. Treat the ink as a fundamental part of your printing process. Control its condition as you would any other aspect of the pressrun—equipment and materials.